
The Makita I’m using can be set between 10 and 30k RPM and that range should work for both smaller and larger tools than what I’m using. I’m running this single-flute endmill at about 20k RPM and I have a feeling that I maybe should even be going a bit faster. Sounds like a lot, but because these machines aren’t really rigid enough to be running ¼” or 6mm endmills, the go-to tooling is ⅛ – and that needs to be run quite fast to cut properly. I do like the simple brushless ER11 spindle that’s now living on the MendelMax Mill, but that only goes up to 12k RPM. Now, aside from form-factor, cost and noise, the biggest factor for whether a spindle is going to work for you is the RPM range. Then there’s the low-end brushed or brushless “spindles” with around 400W of power, which are basically just a motor with an ER11 collet screwed on.Īnd then there’s the brushless water- or air-cooled spindles, typically a kilowatt or more. There’s two, three maybe different types of spindles used in hobby machines.
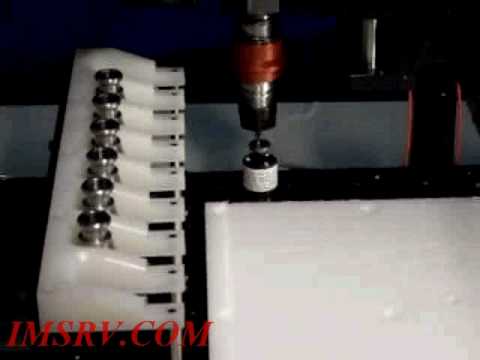
There’s a little adapter sleeve in here because I didn’t nail the router’s diameter first try and I didn’t want to reprint the entire thing. So yeah, made that longer, added two more screws, done. By default, it’s less than half as tall and only uses two screws to attach to the aluminum profile, and as such, it does flex when the router and the endmill engage with your material and produce cutting forces. The other bit is this spindle or router mount. I could have made these parts even more rigid, though. I don’t have a before, but I can take out two bolts and kind of show you the difference. My simple fix for these brackets: Adding two more bolt holes as little ears – these actually fit in all the places where the original part is used, on top of the Z-axis it would look a bit silly, but but with two extra holes drilled on each end of the X and Y axes, those were already significantly stiffened up. Of course, flex like this is deadly for cutting any harder material, and since there is still plenty of flex in the other bits, making this machine more rigid in whatever way you can manage is kind of important. Now, these are the original brackets, and with those, the X and Y axes were incredibly easy to twist about, and you could see the profile actually sliding around on the MDF. So it’s a main aluminum profile that they’ve got some openbuilds wheels running on, a leadscrew in the center, some sort of a carriage that runs on it and then these brackets at the end that either bolt the track to the frame or hold a stepper motor to drive the leadscrew. Especially for 3D printed parts, they really don’t need to be identical, but still, it’s cool to see that multifunction built in. So, Bob has a pretty sleek build with three axes that are built similarly, but also use identical printed parts. Okay, let’s get going with the end brackets here. So let’s go through what issues I tried to fix, what worked and what didn’t. The folks making this open-source router were happy to see some mods, so I went at it and now it cuts aluminum. Bob is a moving-bed CNC router, kinda similar to the Carbide 3D Nomad, and as-is, it was ok, it was usable for light wood cutting and so on, but there were a few things that were bothering me about it, and in my mind, if I fixed those, I would be able to use it for at least cutting aluminum, and that would make it a massively more useful machine for me. And one of those tools is the Sienci Labs Mill One CNC, which for the rest of the video, I’ll call Bob for stupid, but obvious reasons. Today we find ourselves in my former printcave – the printers have moved on to the studio, but I’m keeping the dirtier tools here in the basement.
#DESKCNC BACKLASH MODS#
Here’s the mods and improvements I made to finally get it cutting aluminum! Introduction When building a small engine, the camshaft is one of the more difficult components to make.The Sienci Mill One was a strange tool to start with – bare-bones to be barely usable yet with potential of turning into a much more capable machine. Using the Sherline CNC Cam Grinder P/N 8650 (without computer) P/N 8655 (with computer) The Sherline CNC cam grinder.
